For Part Repairs, Arkansas Shop is on the Case
US, July 11. Tucked away in a quiet corner of a Pratt & Whitney repair facility in northwest Arkansas is a small but mighty team of employees whose job is literally to solve puzzles.
Just not the ordinary coffee-table type.
They’re some of the most challenging engineering riddles being thrown at some of the most experienced engineers and machinists in the entire company. The team’s task: designing creative solutions to build all sorts of fixtures to hold the complex parts of all shapes and sizes in place so that technicians can repair them.
For the talented employees of the Prototype and Tooling shop in Springdale, Arkansas, it’s a task they’ve handled with skill since the shop was acquired by Pratt & Whitney, a Raytheon Technologies business, in the mid-1990s.
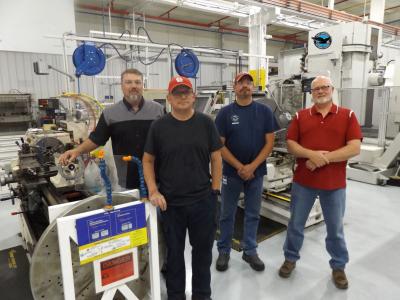
The four machinists who work in the P&T shop – Kevin Darnell, Billy Estes, Joe Hartman and David Framstad – average more than 20 years of experience. Engineering Manager Steve Bardsley and Development Engineering Manager Clinton Steely are proud to say that it takes a “true machinist” to work in a P&T shop.
“Every day you’re doing something different,” said Bardsley. “The team really enjoys it – it’s a big challenge, and requires creative thinking, but it’s also fulfilling.”
The P&T shop is co-located with Pratt & Whitney’s PSD operation, formerly the Nordam Propulsion Systems Division acquired in 1995. It serves as the case repair facility for the Pratt & Whitney Aftermarket network, performing work for both commercial and military customers, supporting repairs for a wide range of engines, including the F135 and GTF.
Bardsley explained that each part that arrives in the shop for repair also needs a corresponding fixture to hold it in place while it’s being inspected and repaired. Parts coming into the shop can range up to 65 inches in diameter and weigh between 300 and 400 pounds. Depending on their complexity, fixtures can take as long as nine months to build.
“Every fixture has to be built unique to the part,” said Bardsley, although recent advances in design and materials have allowed some newer fixtures to be used for multiple setups. These “universal fixtures” have decreased setup times by as much as 30 percent and reduced scrap, waste and overall repair costs.
That’s a huge advantage considering that since 2004, P&T has built an average of 1.5 fixtures per week, or approximately 1,400 in all.
Since most of the P&T group left production jobs to join the team, they retain strong ties to the production shop floor and are familiar with many of the challenges the workers encounter on a daily basis. It’s why many of the designs and process improvements originate from strong two-way communication and collaboration with employees performing the actual repair work.
Steely explained that every repair process is run first in P&T to validate CNC programming, tooling performance and process plans. This enables most first article inspections to be completed prior to parts being run on the production floor. This additional checkpoint improves both initial first pass yield and PSD’s quality signature. “P&T’s ability to work closely with both our development engineers and special process experts is a key value driver,” he said.
“It’s a process that sometimes requires give and take, but has also built a lot of trust between P&T and the production shop,” said Bardsley. “If production associates have a good idea or something they need from us, they simply ask one of our machinists to come into the cell and review their idea. We take it from there.”